Little Known Facts About Alcast Company.
The 5-Second Trick For Alcast Company
Table of ContentsThe Definitive Guide to Alcast CompanyGetting My Alcast Company To Work3 Easy Facts About Alcast Company Shown4 Easy Facts About Alcast Company Shown8 Easy Facts About Alcast Company ExplainedAll About Alcast Company
Chemical Contrast of Cast Light weight aluminum Alloys Silicon advertises castability by minimizing the alloy's melting temperature and enhancing fluidness throughout spreading. Additionally, silicon contributes to the alloy's toughness and put on resistance, making it important in applications where durability is critical, such as auto components and engine components.It additionally improves the machinability of the alloy, making it much easier to process right into finished products. By doing this, iron adds to the general workability of aluminum alloys. Copper boosts electrical conductivity, making it helpful in electric applications. It also improves rust resistance and includes in the alloy's total toughness.
Manganese adds to the stamina of light weight aluminum alloys and improves workability. Magnesium is a light-weight element that offers stamina and influence resistance to aluminum alloys.
The Greatest Guide To Alcast Company
Zinc enhances the castability of light weight aluminum alloys and helps regulate the solidification process throughout spreading. It boosts the alloy's strength and solidity.
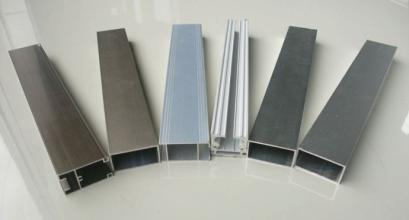
The primary thermal conductivity, tensile toughness, return toughness, and prolongation vary. Select suitable raw products according to the performance of the target product produced. Among the above alloys, A356 has the highest thermal conductivity, and A380 and ADC12 have the most affordable. The tensile limitation is the opposite. A360 has the very best return strength and the greatest elongation rate.
Not known Facts About Alcast Company
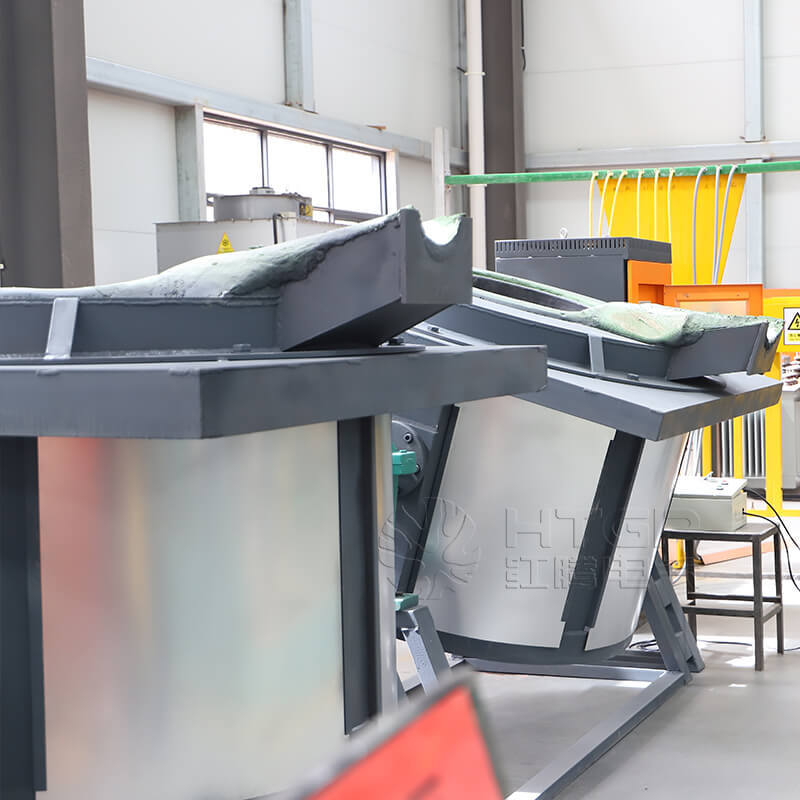
In accuracy casting, 6063 is appropriate for applications where intricate geometries and high-quality surface coatings are extremely important. Examples consist of telecommunication rooms, where the alloy's premium formability enables sleek and cosmetically pleasing layouts while maintaining architectural integrity. In the Lights Solutions sector, precision-cast 6063 elements produce classy and reliable lighting components that require intricate shapes and great thermal performance.
The A360 shows premium elongation, making it ideal for complicated and thin-walled elements. In accuracy spreading applications, A360 is well-suited for markets such as Customer Electronic Devices, Telecommunication, and Power Devices.
The 7-Minute Rule for Alcast Company
Its distinct residential properties make A360 a valuable option for accuracy casting in these sectors, enhancing product durability and quality. Aluminum alloy 380, or A380, is a commonly made use of spreading alloy with several distinct features. It provides exceptional castability, making it an excellent choice for precision spreading. A380 displays good fluidness when molten, making sure intricate and in-depth mold and mildews are precisely duplicated.
In precision casting, light weight aluminum 413 beams in the Customer Electronic Devices and Power Devices industries. It's generally used to craft intricate components like smart device housings, cam bodies, and power device coverings. Its precision is remarkable, with tight resistances as much as 0.01 mm, making certain perfect item setting up. This alloy's remarkable corrosion resistance makes it an exceptional option for outside applications, ensuring durable, durable items in the discussed industries.
Alcast Company Things To Know Before You Buy
The aluminum alloy you select will significantly affect both the casting procedure and the residential properties of the last item. Because of this, you need to make your decision thoroughly and take an informed strategy.
Determining the most appropriate aluminum alloy for your application will certainly mean evaluating a wide variety of characteristics. The first group addresses alloy attributes that influence the production process.
Alcast Company - Questions
The alloy you select for die casting straight impacts several facets see post of the casting procedure, like just how very easy the alloy is to work with and if it is susceptible to casting flaws. Hot breaking, additionally referred to as solidification cracking, is a typical die casting problem for light weight aluminum alloys that can result in interior or surface-level rips or cracks.
Certain light weight aluminum alloys are a lot more prone to hot splitting than others, and your choice needs to consider this. It can harm both the cast and the die, so you should look for alloys with high anti-soldering buildings.
Rust resistance, which is already a significant attribute of light weight aluminum, can differ significantly from alloy to alloy and is a vital characteristic to consider relying on the ecological conditions your product will be subjected to (aluminum casting manufacturer). Wear resistance is one more residential property frequently sought in light weight aluminum products and can separate some alloys